According to the garments workmanship and appearance garments defects are divided in the three ways
1. Critical defects
2. Major defects
3. Minor defects
1. Critical Defects
A critical defect is one that is likely to result in hazardous or unsafe conditions when using the product. A critical defect is also a deviation from delivery requirements which prevents the product from being received. If one (1) occurrence of critical defect is observed during the inspection, the entire lot will be rejected. A 100% inspection will be carried-out by the garments factory QA Staff to remove the defective product/s.
2. Major Defects
A major defect is one that is likely to result in a customer complaint or return. A major defect is also one that will most likely result in product failure after a period of time that is considered unacceptable to the customer or end user. A major defect will usually (but not always) be obvious to the inspector during the visual garment inspection. It will also be obvious to the customer during use.
3. Minor Defects
A minor defect is one that is unlikely to result in customer complaint or return. A minor defect is a deviation from the required standard, but one that is unlikely to affect the usability of the product. A minor defect will usually be seen by the inspector, but may be overlooked by the customer
Garment Defects
1. Broken, skipped or missing stitches
Broken, skipped or missing stitches occur during the sewing process and are usually attributed to either a fault with the sewing machine or a worker error.This can be a visual issue with the product, especially in garments which use different stitching colors, like many jeans you can buy today. Stitching problems may also weaken the structural integrity of the seam, causing premature wear of the product or even ripping of the seam.
Potential reasons for broken, skipped or missing stitches
Broken stitching is often caused by rough handling. If you see stitching is missing or has been skipped, workers at your factory may be rushing to complete an order. The supplier may also have been provided an outdated specification for sewing.Stitch issues will generally be considered a minor defect, but can be major if the issue is evident on a significant portion or highly visible area of the garment.
If you find broken, skipped or missing stitches during inspection of the garments you import, voice your concerns with your supplier. The factory that produces the goods may be able to mend these in a reasonable amount of time before shipping
2. Untrimmed threads
A very common defect, untrimmed threads are a formality in garment production. Ideally, untrimmed threads will be identified and removed during the factory’s final production stage and internal QC check.Although untrimmed threads are generally considered a minor defect, they can become a more serious issue if evident in a significant portion of the order.
The concern of many buyers is that untrimmed threads give the clothing a “cheap” appearance. Untrimmed threads are a sign of sloppy workmanship.
Trimming the untrimmed
The good news is that untrimmed threads are one of the more easy-to-remedy garment defects. The factory making your clothing may need to be more vigilant in looking for this issue and trimming excess material prior to packing and shipping3. Puckering
Puckering is an irregular seam surface. You’ll see this garment defect more commonly in woven fabrics and knitted ones. Puckering is especially prominent on garments that are tightly woven.Causes and remedies for puckering
Puckering can be caused by the characteristics of the fabric but more commonly is related to one of the following issues related to workmanship:- High tension on the thread during sewing, which can cause the fabric to bunch up
- Using a dull needle, which may have difficulty puncturing the fabric, or
- One ply of fabric is fed into the sewing machine at a different rate than other pliƩ
4. Dimensions out of tolerance
Dimensional issues can be related to faulty patterns being used, cutting issues, incorrect stitching or inattention to tolerances by the workers. Incorrect dimensions can be particularly problematic because:- The garment size could be affected, which means the item won’t fit the end-consumer correctly and
- The entire order quantity of that item is likely to be affected
Developing tolerances and points of measure
Issues related to dimensions can easily cause an entire order of product to fail product inspection. The best way to prevent these is to make sure your supplier has the correct tolerances and points of measure.And if you have someone inspecting your product before shipping, make sure they know both the agreed tolerances and measuring methods.
Although many independent inspection firms with garment experience have developed their own tolerances for dimensions, you may have your own you’d like used for inspection. Similarly, you may have your own measuring method, which your inspector may need to be informed of prior to verifying dimensions.
6. Open Seams
Open seams are both visually unappealing and weaken the integrity of the garment seams. They are almost always considered a major defect, regardless of size. Open seams are generally not a defect present in a full order, but will be evident on isolated units due to poor folding or an incorrect technique used by the worker.
Repairing an open seam tends to leave behind obvious signs of mending, such as overlapping stitching. Talk with your supplier if this kind of garment defect is present in a high number of pieces of your order and discuss ways to prevent or mitigate open seams.
5. Incorrect Stitches per Inch
Most garment specifications will specify the stitches per inch (SPI) required. This is because stitching that is less dense can compromise:- Seam strength
- Stitching appearance, and
- Seam elasticity (on stretch fabrics)
Managing stitch count in garments
This garment defect can also be caused by incorrect settings of the machine. A low SPI may also be due to workers intentionally lengthening the stitch in order to speed up the sewing. This is especially common where workers are paid at a piece rate, where greater focus may be placed on quantity, rather than quality.A simple check can be performed to measure SPI with a ruler. If you carry out inspection at the factory prior to shipping, make sure your inspector is measuring and reporting SPI. Then if SPI is found to be out of tolerance, you can address this with your supplier.
Fabric Defects
Woven Fabric Defects
* Coloured Flecks : Presence of foreign mater in the yarn .The reason for this is sometimes cotton fibres getting contamination during the ginning stage with leaves .
* Knot : Is a fastening made by tying together the end of yarns
* Slub : Is bunch of yarns having less twist or no twist and has a wider diameter compared to the normal yarn
* Broken pattern : Is non continuity of the pattern/ design or Weave
* Broken Ends Woven in a Bunch : is caused by bunch of broken ends woven to the fabric
*Bad or defective selvedge:
Bad selvedge in Woven fabric due to the faulty weaving. Here, warp ends being set too far apart for the thickness of the yarn or in finished fabric.
Defective selvedge
2. Broken ends or warp:
A defect in the woven fabric caused by a warp yarn that was broken during weaving or Finishing.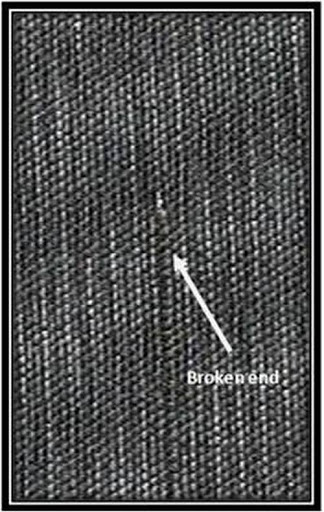
Broken ends
3. Broken picks or weft:
A filling yarn that is broken in the weaving of fabric.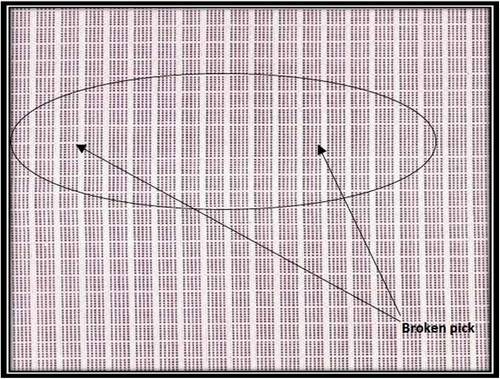
Broken picks
4. Loose warp:
This type of fault is produced in woven fabric when the tension of warp yarn is slow.
Loose-warp
5. Loose weft or snarl:
It is produced in woven fabric due to the looseness of filling yarn.
Loose weft
6. Double ends:
This kind of fault is produced in woven fabric when the two ends of warp sticks get together after sizing.
Double ends
7. Tight ends:
If the tension of warp yarn is more than the other ends present in the loom then this type of fault is produced in woven fabric.
Tight ends
8. Float of warp:
If someone pulls the fabric together the cloth roller intentionally or unintentionally then this kind of defect is produced in woven fabric.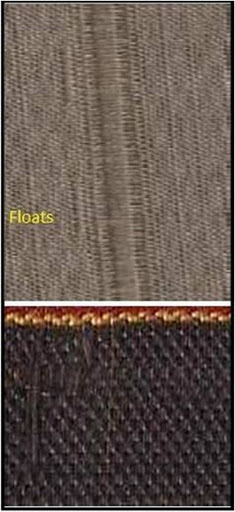
Float of warp
9. Wrong end color:
It is produced in woven fabric due to the wrong drawing of colored yarn.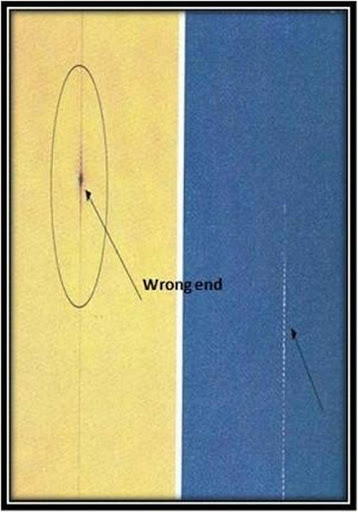
Wrong end color
10. Miss pick:
This kind of defect is produced in woven fabric when operator starts a stopped machine without picking the broken weft from the shade.
11. Double pick:
It is produced in woven fabric when the cutter don’t work properly.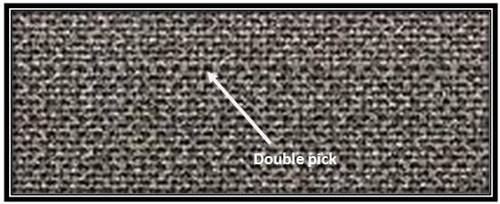
Double picks
12. Weft bar:
When count of yarn varies from one cone to another cone then a bar of weft will be appeared in fabric after weaving.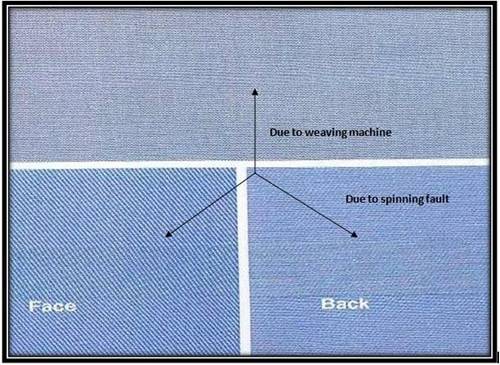
Weft bar
13. Ball:
If the warp is too much hairy then the reed will create ball in warp yarn in between reed and heald shaft. If the ball is small enough to pass through the dent of reed then those will form the ball in fabric.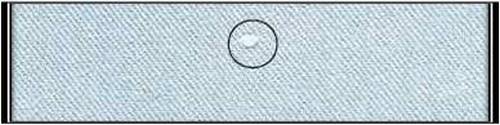
Ball
14. Hole:
A fabric imperfection in which one or several yarns are sufficiently damaged to create an opening.
Hole
15. Oil spot or stain:
Discoloration on a local area of a substrate that may be resistant to remove by laundering or dry cleaning It occurs during spinning, weaving or finishing . It is also often seen in the woven fabric. It is also produced in woven fabric if too much oiling has done on the loom parts.
Oil-stain
17. Thick and thin place:
Fabric defect in which fabric count varies more than a specified percentage from the intended count. If the thick or thin place is more than one inch (2.54cm) wide then it is considered as a major defect in fabric grading.
Thick place
A segment of yarn at least ¼ inch (0.6cm) long that is noticeably thicker than adjacent portions of yarn is called thick place. A segment of yarn at least 25% smaller in diameter than adjacent portions of yarn is called thin place.
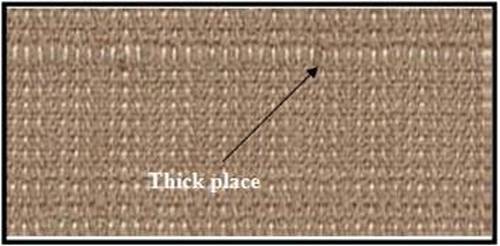
Thick place
17. Temple mark:
If the placement of ring in the temple bar is wrong or the pressure of temple to the fabrics is too high then this type of fault is produced.
Temple mark

Temple mark
18. Reed mark:
In woven fabric, a crack between the groups of warp ends either continuous or at intervals. It’s may be caused by the wrong drawing-in of the warp or damage to the reed wires.
Reed mark
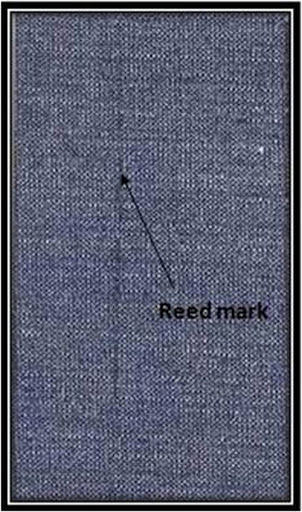
Reed mark
19. Slub:
If the yarn contains unexpected slub in it then those slub will be appeared in the fabric as a fault.

Slub
No comments:
Post a Comment